|
可靠性工程 |
1.可靠性工程培训时间
2月14-15日,5月21-22日,7月22-23日,11月27-28日
2.可靠性工程培训费用与地点
公开课程地点:杭州、上海、北京、广州、成都、南京、苏州。
课程费用:4500RMB/人,3人以上团体报名9.5折优惠,免费赠送MINITAB软件套。可安排进厂内训,受训名额不限。
3.可靠性工程培训报名
4.可靠性工程培训时间
第一章:可靠性基本概念
1、可靠性学科发展历程
2、可靠性的定义
——IEEE可靠性的定义
——装备可靠性的定义
——产品工作可靠性的定义
——广义可靠性
3、可靠性学科研究的内容
4、可靠性设计的主要工作
5、二十世纪留给二十一世纪可靠性工程热点问题
第二章 可靠性基础理论
第一节、可靠性特征量
——定义:
——可靠性特征量指标
——可靠度与不可靠度
——失效(故障)密度函数
——失效率(故障率) Failure Rate
——故障率与可靠度、故障密度函数的关系
——故障率浴盆曲线
——产品的故障率曲线的三个阶段
——产品的寿命特征
——平均故障前时间
——平均故障间隔时间
——可用性定义
——可靠性参数和指标选择的要求和依据
第二节、可靠性数据统计分析的过程及意义
——可靠性数据分析概述
——什么是可靠性数据?
——可靠性数据的来源、
——什么是可靠性数据分析?
——各阶段可靠性数据分析的目的和意义
——可靠性数据库
第三节、统计学基本概念
——统计学术语
第四节、常用的概率分布
第五节、常用的参数估计方法
第三章 系统可靠性模型
第一节 概述
——系统定义
——系统可靠性设计的目的
——影响系统可靠性的因素
——不可修复系统
——可修复系统
——系统的各种模型(原理图、功能框图、功能流程图 、可靠性框图)
——基本可靠性模型
——任务可靠性模型
——典型可靠性模型分类
第二节 不可修系统
——串联系统
——并联系统
——混联系统
——表决系统
——旁联系统
第三节 可修系统
——概述
——维修性特征量
——可用性特征量
——马尔柯夫过程
——典型可修系统可用性
第四章 可靠性分配与预计
第一节 概 述
——可靠性分配
——可靠性预计
——可靠性分配目的
——可靠性预计的目的
——可靠性分配与可靠性预计的关系
——可靠性分配与可靠性预计的作用
——可靠性分配的程序
——可靠性分配的准则
——可靠性分配方法的种类
第二节 可靠性分配
一、可靠性分配的无约束分配方法
——等分配法
——评分分配法
——再分配法
——比例分配法
——AGREE方法
——不同研制阶段的可靠性分配方法
二、可靠性分配的优化方法
第三节可靠性预计
1、可靠性预计目的、用途
2、产品可靠性预计的程序
3、可靠性预计的类型
4、电子产品的可靠性预计
5、可靠性预计的传统方法
——数学模型法
——相似设备法
——相似复杂性法
——功能预计法
——边值法
——元部件计数法
——应力分析法
——边值法(上下限法)
6、可靠性预计方法及其应用范围
7、非指数分布的产品可靠性预计
第五章 故障模式影响与危害度分析(FMECA)
第一节 FMECA概述
——基本概念——故障、故障模式、故障影响、危害度
——FMECA的目的
——FMECA 的步骤
——FMECA方法分类
——在产品寿命周期各阶段的FMECA方法
第二节 故障模式影响分析FMEA
——FMEA分析流程
——系统定义
——故障模式分析
——故障判据
——故障模式分析的工作内容
——故障模式分析的方法
——典型故障模式
——机械产品典型故障模式(案例)
——故障原因分析
——故障影响分析
——故障严酷度
——故障检测方法分析 (可探测性)
——补偿措施分析
第三节 危害度分析CA
——CA的目的
——风险优先数法
——危害矩阵法
——危害性矩阵图
——CA的实施
第四节 FMECA结果形式
——FMECA报告应包含的内容
——可靠性关键重要产品清单
第五节 FMECA应用示例
第六章 故障树分析Fault Tree Analysis
第一节 概述
——故障树的定义
——故障树分析
——故障树分析常用的术语及符号
——故障树分析常用的逻辑门及符号
第二节 建立故障树的方法
——建立故障树的步骤
——故障树的规范化
——故障树简化方法-模块化方法
——故障树简化方法-布尔代数法
第三节 故障树的定性分析
——故障树的结构函数
——最小割集和最小路集
——故障树分析的下行法与上行法
——故障树的对偶树
第四节 故障树的定量分析
——概率组成函数穷举法
——利用最小割集求解
——概率重要度
——故障树的对偶树
第五节 故障树分析的发展方向
——模糊故障树
——动态故障树
——贝叶斯网络与故障树分析
——多状态故障树
第七章 机械可靠性设计原理
第一节 机械可靠性设计概述
——机械可靠性发展概述
——机械可靠性问题的分类
——机械可靠性的特点
——传统的机械设计与机械可靠性设计的区别
——机械零件可靠性设计的特点
——机械可靠性设计的过程
——机构可靠性简介
第二节 应力——强度干涉理论
——广义的应力
——广义的强度
——基于统计的可靠性定义
——基于模型的可靠性定义
——应力-强度分布曲线与时间的关系
——干涉概率的计算方法-概率密度联合积分法
——干涉概率的计算方法-强度与应力之差概率密度函数积分法
第三节 机械零件静强度可靠性设计
——基本步骤:
——设计参数的统计处理与计算
——零件强度分布规律及分布参数的确定--材料性能的统计分析
——强度分布的确定
——已知的分布规律
——材料性能的变异系数
——材料拉伸屈服极限的均值和标准差
——现有手册中强度数据的取用
——强度分布参数的近似算法
——确定零件尺寸分布
——零件横截面上的工作应力
——确定应力分布的方法
——代数法确定应力分布类型和分布参数
——随机变量函数的均值和标准差的近似计算
——矩数法确定应力分布
——受拉零件的静强度可靠性设计
第四节 机械零件疲劳强度可靠性设计
——疲劳破坏的基本概念
——材料的疲劳性能
——疲劳载荷的统计与分析
——稳定变应力下的疲劳强度可靠性计算
——累积损伤理论简介
第五节 机械零件磨损强度的可靠性设计
——磨损的基本概念
——磨损曲线
——花键磨损量与时间的关系
——磨损速度和磨损量的计算
——磨损寿命曲线
——磨损寿命曲线的应用
——给定工作寿命时零件耐磨性可靠度计算
——给定可靠度时零件耐磨寿命的计算
第六节 机械零件腐蚀可靠性设计
——腐蚀
——均匀腐蚀的概率计算(与稳定磨损期算法相同)
第七节 机械零件结构稳健可靠性设计
第八章 机械可靠性优化设计
——优化设计的基本概念
——机械可靠性优化设计的意义
——机械可靠性优化设计的数学模型
——机械可靠性优化设计例题
——复杂系统可靠性优化设计问题
第九章 可靠性试验与综合评定
第一节 概述
——可靠性试验方法分类
——工程试验的目的和适用范围
——可靠性统计试验的目的和适用范围
——案例
第二节 环境应力筛选试验
——环境应力筛选试验的相关标准
——环境应力筛选试验
——电子设备可视缺陷分类
——环境应力筛选效益
——故障器件损耗代价比较(US Dollar)
——环境应力筛选试验的类型
——各种筛选能发现的典型缺陷
——环境应力筛选试验比较
第三节 可靠性增长试验
——可靠性增长
——可靠性增长试验
——可靠性增长过程示意图
——可靠性增长试验对象
——可靠性增长试验的步骤
——可靠性增长试验的意义
——有无可靠性增长要求时寿命周期费用的比较
——可靠性增长的数学模型
——Duane 模型
——AMSAA模型
——AMSAA模型的应用
第四节 可靠性统计试验
——可靠性统计试验的类型
——可靠性统计试验中的特性参数
——可靠性统计试验的方案的选择
——概率比序贯试验
——概率比序贯试验试验方案
——概率比序贯试验过程
——概率比序贯试验方案
——概率比序贯试验
——概率比序贯试验方案
第五节 寿命试验
——寿命试验的目的
——产品的寿命参数
——产品寿命试验的分类
——机械可靠性试验技术研究现状
——机械可靠性试验的特点
——机械可靠性试验的关键技术
第六节 系统可靠性评定
——可靠性评定问题的提出
——可靠性评定的意义
——可靠性评定的步骤
——可靠性评定方法
——单元级产品可靠性评定方法
——系统级产品可靠性评定方法
第十章 电子产品可靠性设计分析方法
——概述
——电子元器件的选用
——电磁兼容设计
——热设计
——降额设计
——冗余设计
——耐环境设计
——潜在通路分析
——容差设计
培训案例:
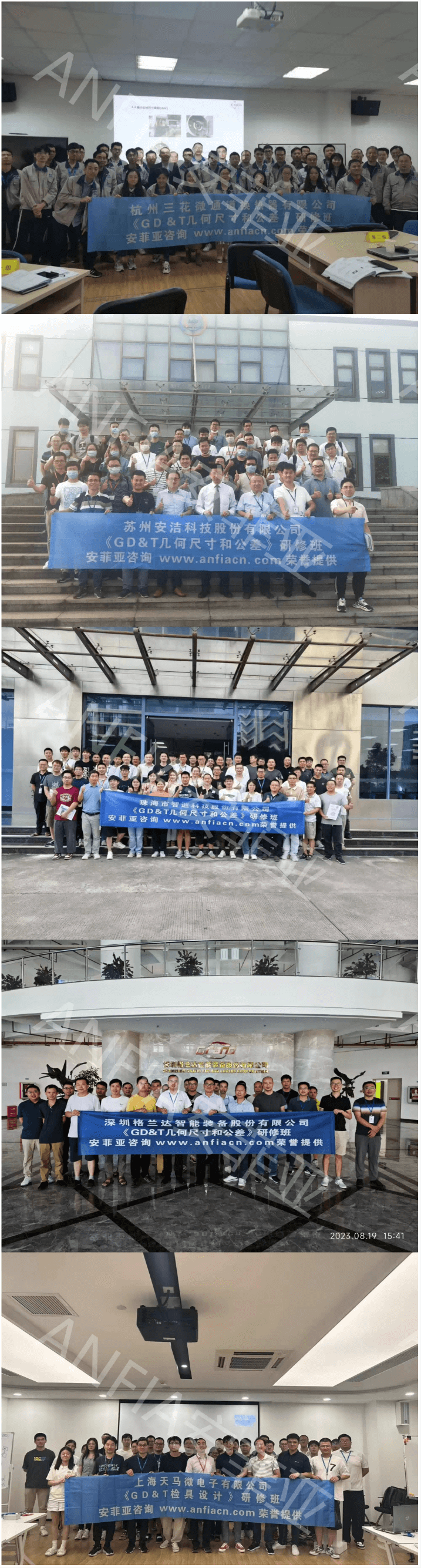
阅读本文的人,还阅读了:
|
|