1.FMEA培训开课地点:
杭州、北京、广州、上海每月定期滚动开班,可根据企业实际情况提供进厂培训
2.FMEA培训时间(二天课程)
2024年1月11-12日,2月27-28日,3月27-28日,4月22-23日,5月27-28日,6月28-29日,7月22-23日,8月27-28日,9月25-26日,10月28-29日,11月26-27日,12月22-23日。
3.FMEA培训班费用
3200RMB/人(含培训费、教材、发票、证书、茶点),3人以上团体报名可9.5折优惠,进厂培训按课时收费,参训人员不限。
4.FMEA培训班报名
点击下载 报名回执,填写后发邮箱 sale01@anfiachina.cn
即可

5.FMEA培训视频
6.FMEA培训班概要
2008年11月AIAG发布《FMEA潜在失效模式与后果分析》第四版手册,并在全球开始生效使用。此FMEA培训班主要讲解DFMEA、PFMEA编制方法、其他工具的链接、FMEA的审核技巧、第四版手册变化点等内容。
此FMEA培训课程将结合安菲亚咨询丰富的实战资询与审核案例,系统地讲解新版FMEA(第四版)的内容、要求、FMEA信息流、与APQP关系、FMEA实施步骤和方法;包括P图、设计矩阵表、特性矩陈图、过程流程图、PFMEA、DFMEA, DVP&R, 边界图、接触面矩阵图、DRBFM(基于失效模式的设计评估)、控制计划等工具,通过FMEA培训帮助学员了解整个实施FMEA的过程全过程内容。克服第四版手册之前的仅填写“FMEA表格”的错误理解与方法。掌握产品APQP开发过程中如何确保失效模式得到考虑并实现失效的控制和预防的方法。
7.FMEA培训班授课对象:
APQP工艺开发设计人员、质量检验员、质量工程师、质量主管、生产部主管、产品设计人员、设计部门主管、采购人员、供应商管理SQE人员。
8.FMEA培训班培训目标:
.理解失效模式和后果分析(FMEA)概念、要求、FMEA信息流、FMEA实施步骤和方法;
.如何通过边界图和P白噪声图,正确界定FMEA的范围与噪声因子;
.应用接触矩阵图,分析部件间在物体、能量、信息、物质形态四个方面的交互作用;
.如何建立参数图P-图,分析产品的错误状态,分析致使产品不可靠的原因;
.如何通过过程流程图与特性矩陈图,建立产品特性KPC和过程特性KCC的对应关系;
.具备运用FMEA、过程控制计划等工具,提高产品和过程的可靠性;
.掌握新版FMEA(第四版)的更新的内容和要求
.理解FMEA与其他任务和工具如APQP工具之间的关系;
.理解FMEA的动态文件,保持及时更新FMEA数据。
9.FMEA培训班课程背景
FMEA最早应用于航空与航天工业,人类的阿波罗登月计划中,就用到FMEA工具思想,现在被广泛运用 于汽车工业中。由三大汽车公司所组成的AIAG机构编写了FMEA手册。为汽车零部件设计、制造过程的质量风险控制与早期标识提供了很好的指南。第四版FMEA手册增加了些具体实例,如边界图、P白噪声图等。在APQP过程中,只有很好的活用FMEA工具,才能将产品的质量风险控制到最低程序,确保产品得到客户的满意。
10.FMEA培训特色
用客户的产品为案例,学员以小组的方式,通过某个大家熟悉的产品案例,学习界限图、接触矩阵图、P图、DRBFM为DFMEA奠定基础;学习过程流程图、特性矩阵图、过程变差识别和过程参数控制,为PFMEA奠定基础;掌握新版FMEA的更新内容和要求;帮助学员学会真正将FMEA作为工程师必需掌握的设计工具。
11.FMEA培训教材
每位参加人员将获得一套安菲亚咨询版权的培训手册。
12.FMEA培训大纲
潜在失效模式和后果分析FMEA
一、基本概念
1、引言
2、什么是FMEA
3、FMEA的发展历史
4、FMEA为什么做不好的原因
5、FMEA的基本流程与方法
6、FMEA的种类
7、DFMEA与PFMEA的区别要点
8、FMEA的实施要点
9、失效模式
10、失效的原因分析(二个层面、五个方面)
11、FMEA的作用
12、过程流程图、FMEA和CP的关系
13、多功能小组
14、脑力风暴
15、RPN流程
16、FMEA常见的问题
二、设计失效模式和后果分析(DFMEA)
1、DFMEA开展的时机
2、DFMEA顾客的定义
3、DFMEA的潜在失效模式
4、严重度评级
5、频度评级
6、不可探测度评级
7、DFMEA的第一步
8、DFMEA的第二步
9、DFMEA的其他输入
10、零件功能表
11、DFMEA典型的失效模式
12、DFMEA典型的失效后果
13、失效的起因和后果
14、失效的影响
15、严重度和分级
16、失效原因和频度
17、现行设计控制和不易探测度
18、风险顺序数(RPN)
19、措施
三、过程失效模式和后果分析
1、PFMEA介绍
2、PFMEA目的
3、PFMEA的顾客定义
4、PFMEA的时机
5、PFMEA的第一步:创建过程流程图
6、过程失效模式和影响分析
7、P-FMEA的输入
8、P-FMEA输出
9、P-FMEA的建立
10、潜在失效模式
11、潜在影响、严重度和分级
12、失效原因和频度
13、失效原因和频度
14、当前过程控制和不可探测度
15、P-FMEA:风险顺序数 (RPN)
四、案例分析
13.FMEA培训日程
日程
|
议题
|
内容
|
开始
|
结束
|
时长
|
第1天
|
FMEA 概述
|
FMEA的背景与历史
|
9:00
|
10:30
|
1:30
|
FMEA与可靠性、FMEA与风险分析
|
FMEA的定义
|
FMEA的种类: SFMEA, DFMEA, PFMEA
|
FMEA小组
|
DFMEA与PFMEA的关联
|
PFMEA开发的时机
|
FMEA的基本步骤:AIAG与VDA的不同描述
|
课间休息
|
10:30
|
10:40
|
0:10
|
PFMEA输入
|
过程流程图
|
10:40
|
12:00
|
1:20
|
特性矩阵表
|
过程流程图与PFMEA的关系
|
PFMEA的两个假设:与产品设计和供方的关系
|
宏观流程图与微观流程图
|
练习:选择熟悉的产品制造过程,编制宏观过程流程图,在其中选择两个相邻的工序作为PFMEA练习的对象,写出微观流程图。
|
午餐
|
12:00
|
13:00
|
1:00
|
PFMEA风险分析
|
PFMEA表格、表头解释
|
13:00
|
14:30
|
1:30
|
过程的功能与要求:条件要求、结果要求、后果要求
|
失效模式开发:与功能/要求的关系、失效模式的定义与标准化、失效模式的充分性
|
失效后果分析:
与失效链的关系、与DFMEA的关系、与专业知识的关系、与相关的失效模式的关系
|
课间休息
|
14:30
|
14:40
|
0:10
|
PFMEA风险分析
|
严重度评价:
· 安全法规、基本功能和次要功能、感官功能的理解
· "对顾客的影响""对制造的影响"的差异与使用
· 质量风险、交付风险、成本风险
· AIAG、VDA、PSA不同的评价准则
· 贝尔缺陷分级原则
|
14:40
|
17:00
|
2:00
|
级别:特殊特性
|
练习:以练习1为基础
描述两个工序的功能与要求、识别失效模式、分析失效后果、研讨严重度评价准则,评价严重度小组发表与培训师讲评
|
第2天
|
PFMEA风险分析
|
潜在原因分析:与门/或门、与供应商质量的关系、常见的错误描述方式、原因的层次与数量、PFMEA是否存在SFMEA?
|
9:00
|
10:30
|
1:30
|
练习3:继续之前的练习原因分析
|
课间休息
|
10:20
|
10:30
|
0:10
|
PFMEA风险分析
|
预防性控制措施开发:与发生率(频度)评价的关联、"现行"的含义、与制造设计规范的关联、常见的过程控制措施(防错、DOE……)
|
10:40
|
12:00
|
1:20
|
探测性控制措施开发:探测对象(失效模式还是原因)、检验与防错
|
频度分析:经验数据域频度的关系、准则的理解,"1"的理解
|
探测度分析:检验的时机与手段、准则的理解、"1"的理解
|
午餐
|
12:00
|
13:00
|
1:00
|
PFMEA风险分析
|
练习4:继续前述练习
· 完成控制措施分析(预防与探测)
· 完成频度评价
· 完成探测度评价
· 完成RPN
· 发表与培训师讲评
|
13:00
|
15:00
|
2:00
|
PFMEA风险控制/改进
|
风险控制原则
|
多方位风险分析
|
改进措施与SOD评价
|
动态管理
|
练习5:
· 继续完成改进措施,或者
· 在给出的, PFME, , , , , A中找错。
|
|
课间休息
|
15:00
|
15:10
|
0:10
|
控制计划
|
控制计划的基本概念
|
15:10
|
17:00
|
1:50
|
过程流程图、控制计划与PFMEA的关联
|
控制计划的编制要求
|
PFMEA变更与控制计划变更的关联
|
答疑与控制计划找错练习
|
|
|
总时长
|
16:00
|
14.培训相关案例
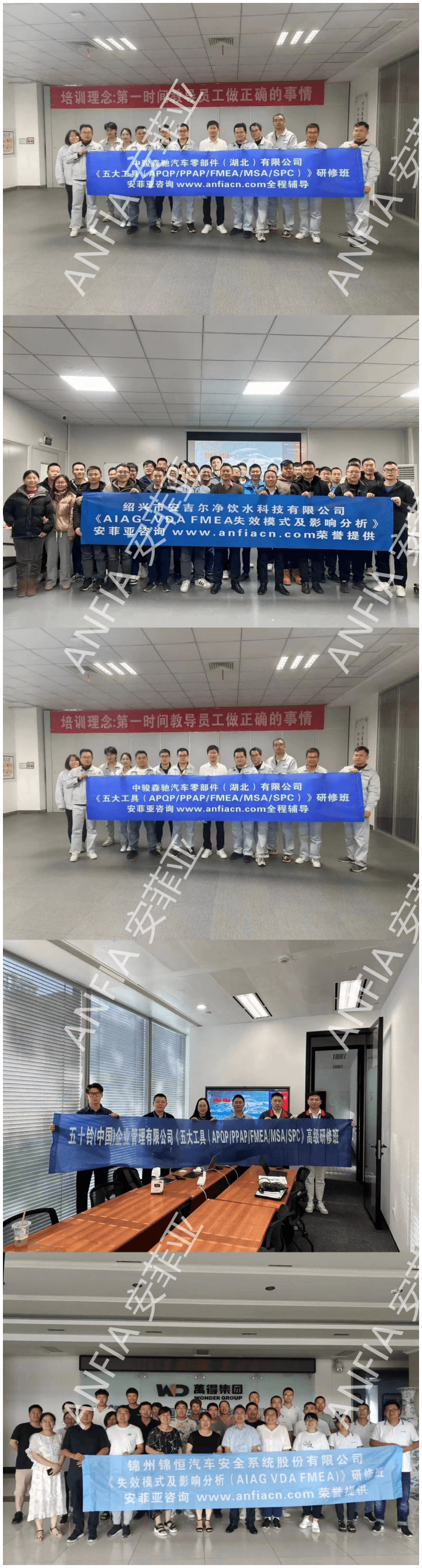
阅读本文的人,还阅读了: